We have a rigorous quality and process control system based on four priorities: food safety, food defense, food quality, and food communication.
Our business operation and sustainability
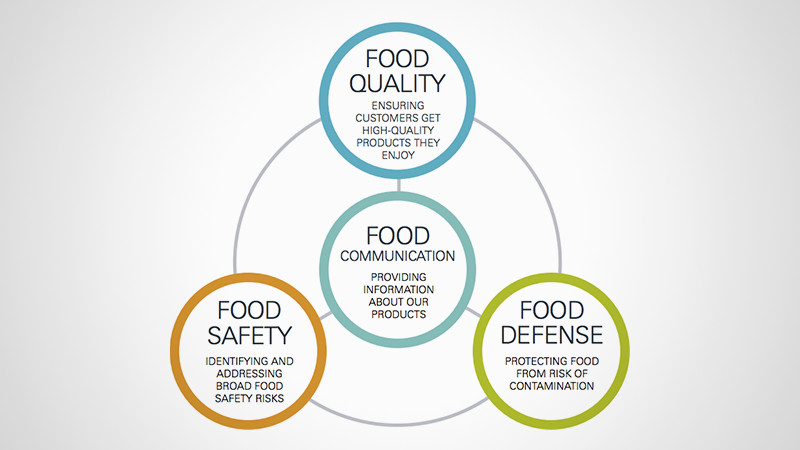
Food safety standards
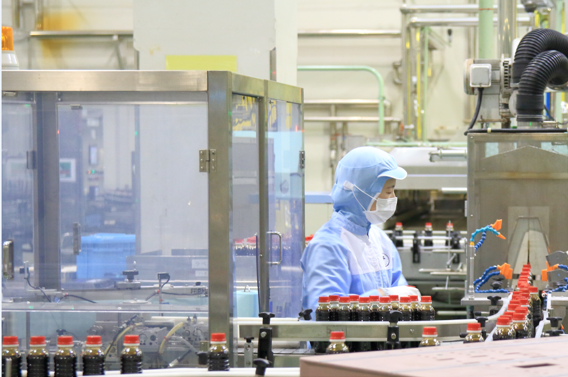
Our processed food business has 26 factories, which produce a variety of food products, from frozen and ambient foods and seasonings. Eighteen of these factories are located in Japan, and eight are located in China, Indonesia, Thailand, and the U.S. Our products are sold primarily in the Japanese market.
We make sure that all of our factories* are certified to the global food safety standard FSSC 22000. FSSC 22000 is recognized by the Global Food Safety Initiative (GFSI), the food industry’s global body for promoting food safety management.
All the factories contracted to manufacture our products are requested to meet food safety standards such as ISO 22000 or FSSC 22000, as an assurance that an adequate food safety management system is in place.
We also work with multiple independent advisors, who have helped to develop our approach to food safety since 2008. Throughout the year, these advisors provide useful information. In 2022, they gave presentations to our employees on industry topics such as food safety, consumer consciousness, and/or the laws and regulations relating to the Food Sanitation Act. These events provided employees with a greater awareness of new developments and important topics in the field of quality control.
In order to ensure food safety, we have introduced a system that records information about our products at every stage of the process, from the raw materials and production to processing, distribution, and sales. This means we can retrace our product to any point, if necessary.
- * One of our factories, which started its operations in 2020, is on track to receive this certification.
Food defense practices
Food defense is about protecting our manufacturing processes and products from intentional contamination. We apply robust food defense guidelines across the supply chain, both in our own factories and our contracted factories. We also carry out annual audits to check how well these guidelines are being implemented.
We are continuously strengthening our food defense mechanisms. We are working on further utilization of factory cameras and enhancement of our drug management system both in our own factories and our contracted factories.
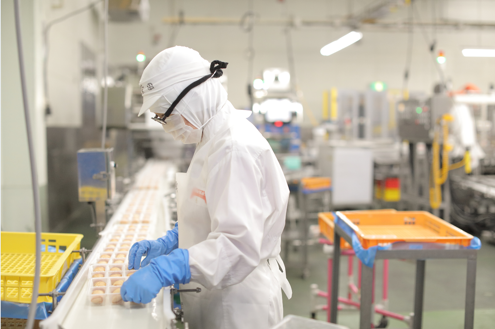
Enhancing food quality
Food quality control is an essential element of our daily operations. Along with quality improvement efforts on factory floors, we ensure that all of our employees receive training through customized e-learning materials.
We also listen to our consumers’ suggestions for improving product quality, and swiftly share these with our factories and operations.
Our internal Quality Assurance Committee enables us to effectively respond to our consumers’ recommendations. The Committee includes not only members of the Quality Control division, but also representatives from many other divisions, such as Product Development, Manufacturing, Distribution, and Marketing and Sales.
Our consumer complaints management system is based on ISO 10002, the international standard for customer satisfaction and complaints handling. To enhance the quality of our correspondence with consumers, in 2016, we introduced a voice transcription system at our Consumer Call Center. This system transcribes and records correspondence with our consumers on behalf of our operators, enabling the operators to focus on providing excellent customer service.
Further food communication
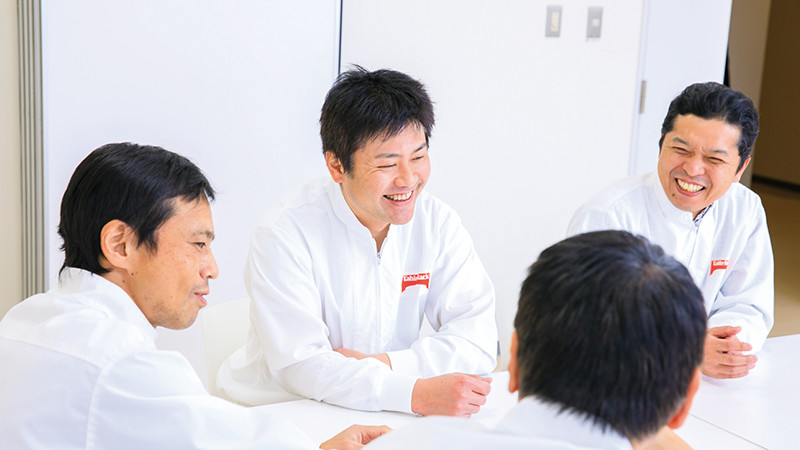
Transparency is at the heart of our business, and we are always willing to provide details about our food products. We respond to consumers’ requests for information and disclose the precise factory where food products were made, or the country of origin of the main ingredients.
We have toll-free numbers on our product labels which consumers can call for extra information. In addition, in order to respond to customer feedback more quickly, TableMark Co., Ltd. is improving the inquiry form on its website year by year.
We seek to provide safe and delicious food for consumers, in the hope that they will choose our products for their loved ones. This principle is not limited to our R&D and manufacturing sites; it applies across all of our operations. We understand the importance of listening to consumers, and have introduced a new online tool to share consumer feedback with all of our employees. We will continue to embed and reinforce this consumer-centric approach throughout our operations.
Reducing our environmental impacts
Biomass co-generation system
As part of our efforts to reduce environmental impacts within our operations, one of the companies within the JT Group, Thai Foods International, built a biomass co-generation system for its Thai factory, where it manufactures seasonings.
The system, which started its operations in 2020, uses rice husks as an alternative fuel source. This system is expected to significantly reduce purchased electricity usage and the resultant Scope 2 greenhouse gas (GHG) emissions by 6,300 tons per year.
This project, which has been adopted by the Joint Crediting Mechanism of the Ministry of Environment in Japan, not only helps us to reduce energy costs but also contributes to GHG reduction in Thailand.
Eco-friendly packaging initiatives
Removing the inner film
We have removed the inner film from the packaging of our "Okonomiyaki" range of Japanese savory pancakes. Through this initiative, we have reduced the amount of plastic raw materials we use annually by approximately 31 tons. This change also reduced our CO2 emissions by approximately 145 tons.
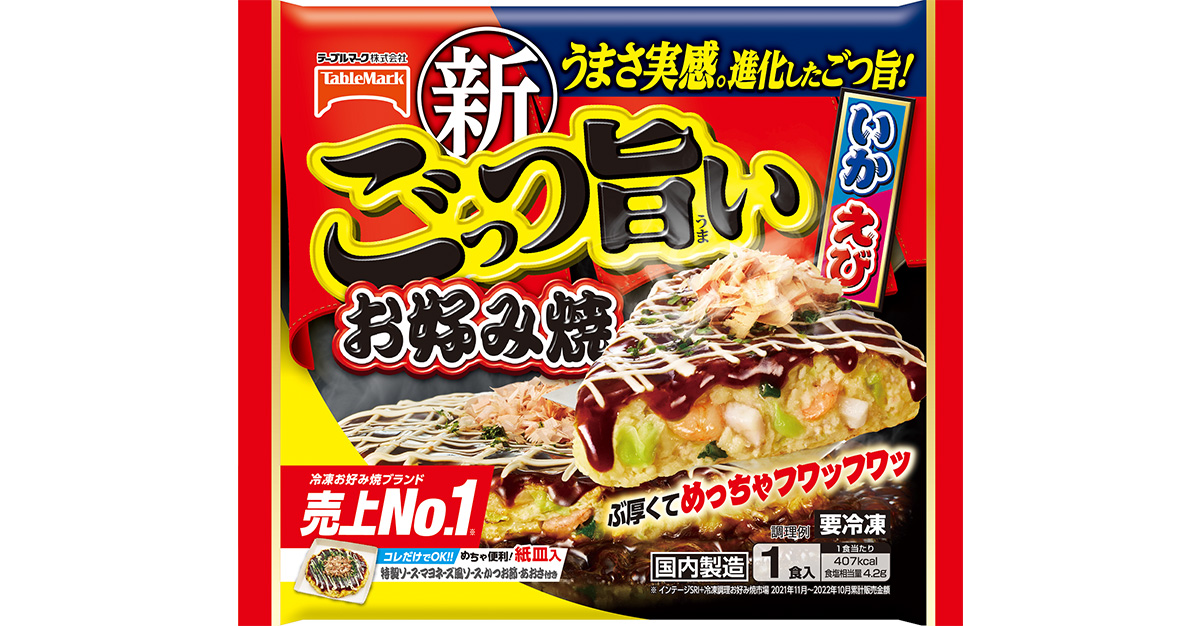
Before
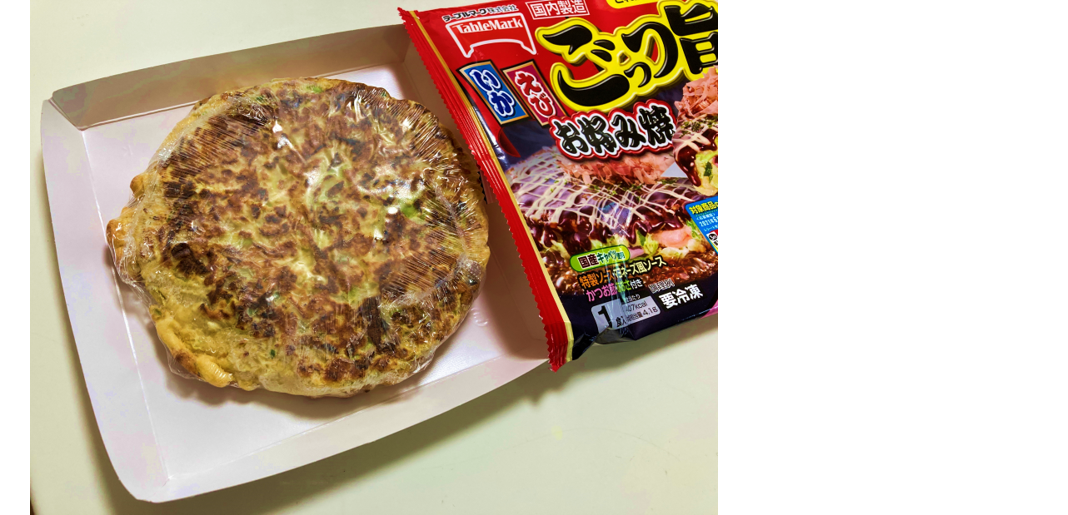
After
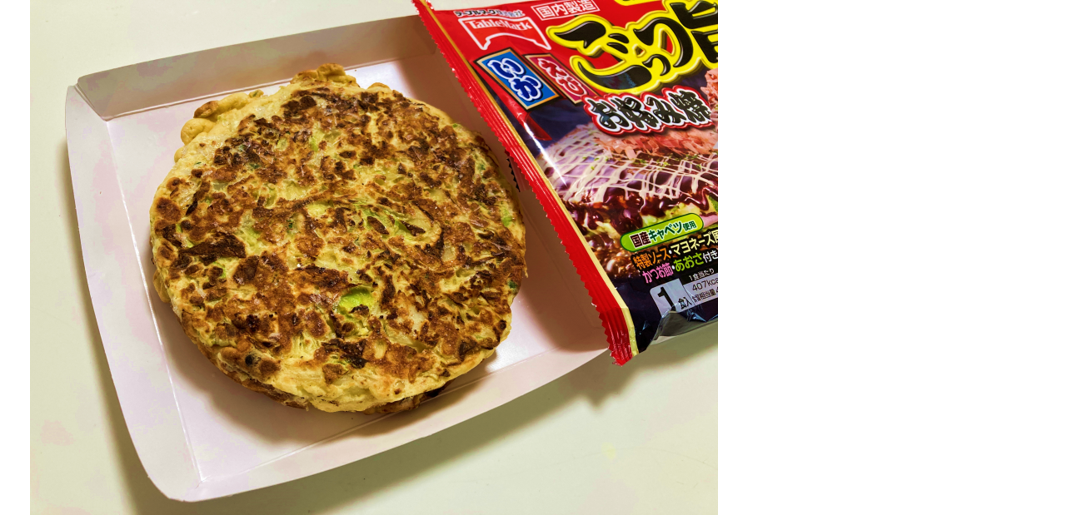
Biomass plastic as a raw material for the packaging
A by-product of rice milling is crushed rice: rice that is broken during the milling process and can no longer be used for manufacturing. In a first for the industry, we are now using the domestic carbon-neutral biomass plastic RiceResin®*, which contains 10% crushed rice generated by our Group, as a raw material for the packaging of some of our cooked rice products. In addition to using RiceResin®, we have reduced the amount of petroleum-based plastic in our packaging by around 4.2% compared to conventional products. We have done this by making the exterior film even thinner.
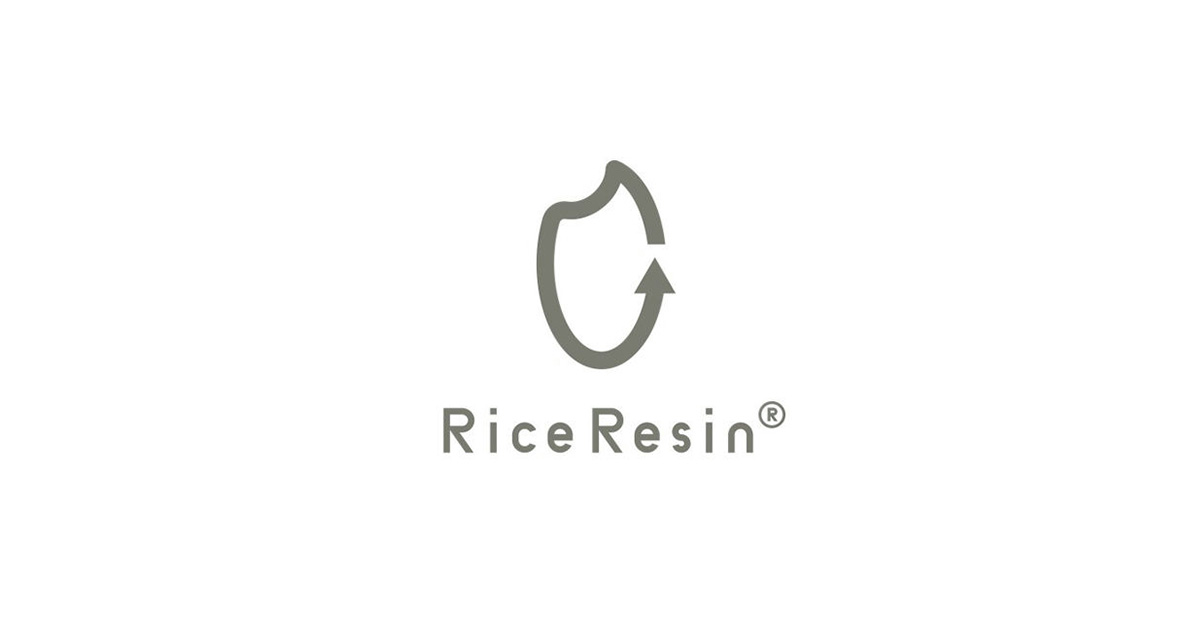
- * RiceResin® is a registered trademark of Biomass Resin Minamiuonuma Co., Ltd. Old rice that is not edible and crushed rice generated during rice milling are upcycled into plastic using new technology.